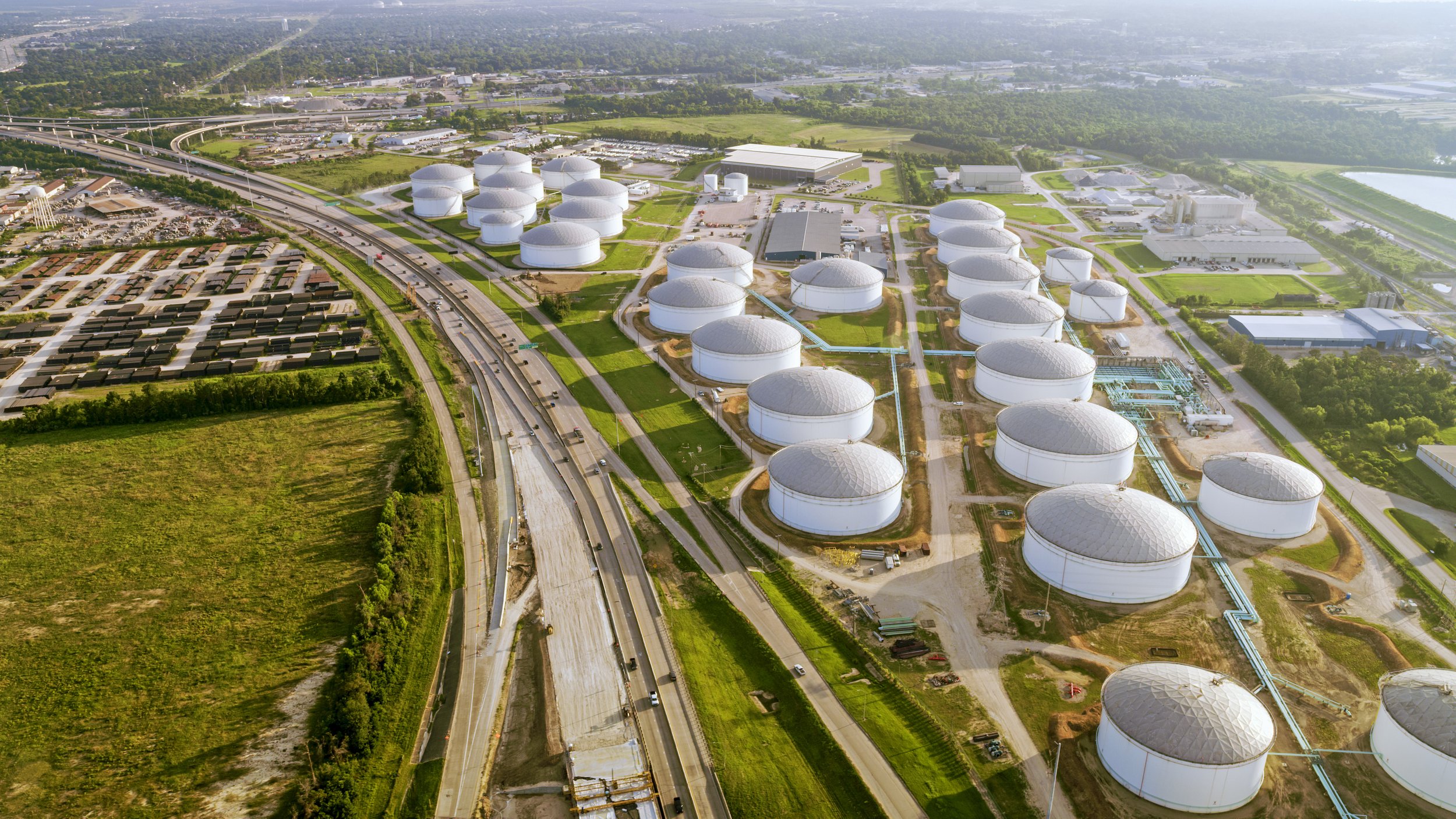
Partner together
Trident Inspection provides a comprehensive range of conventional Non-Destructive Examination (NDE) services for Projects & Turnarounds. Additionally, we offer specialized services through subcontracted personnel, ensuring a tailored approach to meet the unique needs of our clients.
Trident Inspection provides qualified and competent inspectors who are suitably trained and sufficiently experienced to owner-user clients.
Trident Inspection also provides customers with Non-Destructive Examination associated with new construction and maintenance projects in accordance with National and Provincial Regulatory requirements.
These services are provided individually or as a group depending on the customers inspection requirements and needs.
INSPECTION SERVICES
CONVENTIONAL NDE
MAGNETIC PARTICLE
-
MT a non-destructive testing process where a magnetic field is used for detecting surface, and shallow subsurface discontinuities in ferromagnetic materials. Examples of ferromagnetic materials include iron, nickel, cobalt, and some of their alloys. The presence of a surface or subsurface discontinuity in the material allows the magnetic flux to leak since air cannot support as much magnetic field per unit volume as metals.
-
• Can be used on a wide variety of materials.
• Considered a low cost NDE method compared to other methods.
• Indications are visible directly on the material surface.
• Easily portable.
• Very good sensitivity to defects/discontinuities.
• Can examine materials/parts with irregular shapes/geometry.
-
• Depth detection of defects/discontinuities cannot be evaluated without supplemental NDE methods.
• Surface must be accessible and clean and free of oil, grease, scale etc.
• Can only detect surface defects/discontinuities.
ULTRASONIC
-
Ultrasonic examination (UT) is a widely utilized examination method that induces high frequency sound energy into the test specimen. Detection of flaws in components and weldments as well as measuring material thickness are well defined using this method.
-
• Ultrasonic testing can be used as an examination technique while the equipment/component is in or out of service. This advantage makes it a very cost-effective technique to ensure integrity while operational status is not disrupted to the client.
• It can be used to detect, locate, and evaluate defects/flaws that other NDE methods are not best suited for.
• High frequency sound energy allows for high penetrating power for detection of defects/flaws located deep within a given material.
• High sensitivity for the detection of smaller flaws within the material of interest.
• Access to one side of the inspected material only.
• Equipment is very portable, battery operated and intrinsically safe.
• Minimal part/material preparation is needed.
• Compliments other NDE techniques i.e. MFL tank floor scanning.
-
• Surface roughness, material geometry or extremely thin materials make examination difficult to perform.
• Coarse grained materials i.e. cast iron are difficult to inspect due to low sound transmission and high signal noise
• Linear defects/flaws that are located parallel to the sound beam may go undetected.
HARDNESS TESTING
-
Hardness testing measures a material’s resistance to permanent deformation at its surface, by pressing a harder material into it. It is used in several industries for material comparison and selection, as well as quality control of a manufacturing or hardening process.
-
An automated hardness testing machine allows hardness to be measured relatively simply.
To provide meaningful hardness readings for a wide variety of materials, from soft to hard.
For some applications, the hardness of a material is the key characteristic to know. This can be measured directly, rather than inferred by a physical property.
-
It is necessary to have properly prepared the surface of the sample to be measured, usually by grinding and polishing. The surface condition has a significant influence on the hardness reading, so improper surface preparation can give inaccurate or spurious readings.
Most hardness tests are designed for flat surfaces, so curved surfaces do present a challenge. There are some correction factors that need to be applied to compensate for an indentation on a curved surface.
The size of the indentation can be difficult to ascertain objectively, particularly when manually reading the size of micro impressions through an eyepiece. This is mainly an issue with older machines. The latest models have cameras and software packages to automatically focus correctly and display the edge of the impression clearly on a connected computer screen.
If the prescribed minimum distances between indentations are not followed according to the testing standards, the results of the hardness test will be affected. This is also true of an indentation too close to the edge of a sample.
LIQUID PENETRANT
-
Liquid or dye penetrant examination (PT) is a non-destructive testing method that uses capillary forces to locate surface-breaking flaws such as cracks, laps and porosity. The flaw must reach the surface to be tested, but liquid penetrant testing offers an inexpensive solution for testing large areas quickly.
Liquid penetrant testing can be used on any solid, non-porous and clean material, including ceramics, metals, or plastics. This includes both magnetic and non-magnetic metals as well as those that are both conductive and non-conductive. It is frequently used to assess for flaws in castings, forgings, and welded parts – including corrosion tests.
-
• Can be used on a wide variety of materials.
• Considered a low cost NDE method compared to other methods.
• Indications are visible directly on the material surface.
• Easily portable.
• Very good sensitivity to defects/discontinuities.
• Can examine materials/parts with irregular shapes/geometry.
-
• Depth detection of defects/discontinuities cannot be evaluated without supplemental NDE methods.
• Surface must be accessible and clean and free of oil, grease, scale etc.
• Can only detect surface defects/discontinuities.
POSITIVE MATERIAL IDENTIFICATION
-
PMI testing, also known as Positive Material Identification Testing, is the analysis of materials to determine the chemical composition of a metal or alloy at particular (usually multiple) steps of alloy manufacturing or in-process alloy installation. Knowing the exact composition and grade of an alloy enables suppliers, plant workers, and other parties in the chain of custody to match alloy specifications for specific properties such as heat resistance, corrosion resistance, durability, etc.
ASSET INTEGRITY
Corrosion surveys
-
Trident Inspection technicians combine their training, experience, and knowledge of corrosion damage mechanisms and ultrasonics to conduct a detailed and comprehensive yet cost-effective corrosion survey for our clients. We utilize both point readings and general scans to accurately calculate corrosion rates and give clients the ability to understand the corrosion profile when present. Our technicians are trained to recognize and characterize data and relay that information to the client. Our technicians understand the importance of meaningful inspection data, expanding the search area when corrosion is found, and knowing the proper locations to check for corrosion. Predictive failure analysis ensures maximum coverage with minimum inspection costs by ensuring inspection locations are in the right areas. Full T-min code calculations can be performed, and all reports are very well documented to provide clients with critical information at a glance.
API VISUAL INSPECTIONS
-
Trident Inspection Inc. provides Alberta In-Service Pressure Vessel Inspectors (IPV) and Pressure Equipment Vessel / piping Inspectors (API 510 / API 570) to Owner-User clients (AB-512) to aid in the management of their pressure equipment integrity management program.
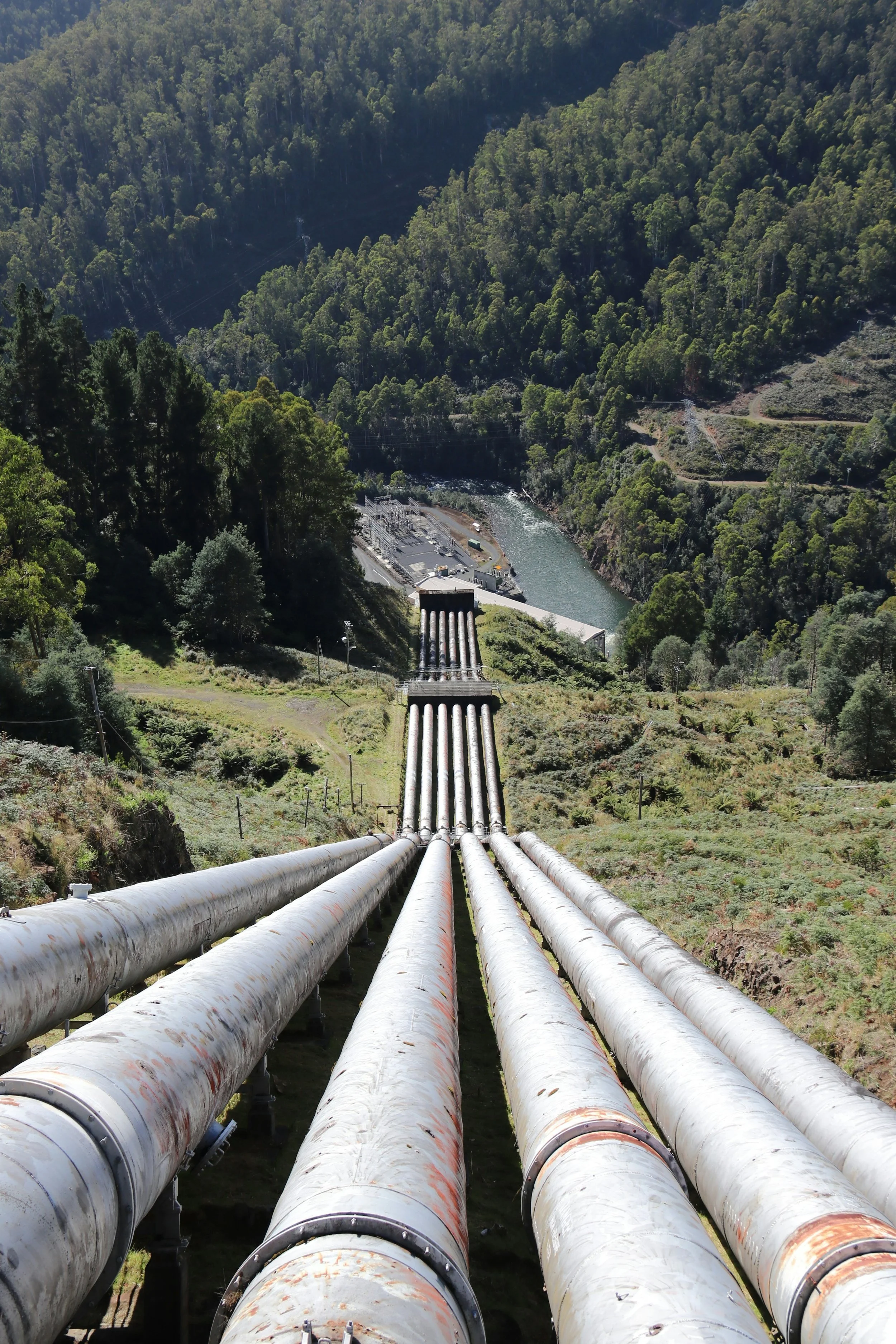
Contact Trident Inspection for all your inspection / Non-Destructive Examination NEEDS.
Trident Inspection provides services associated to new construction, maintenance, and turnaround projects.